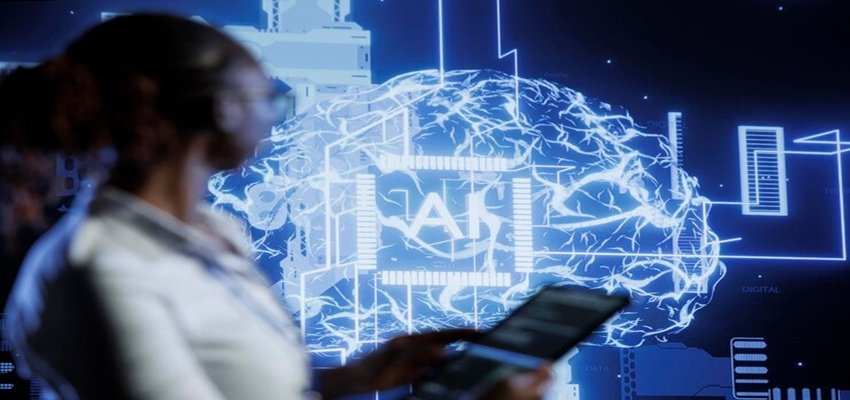
In manufacturing, precision is critical.
Yet traditional AOI systems, designed for early 2000s technology, are struggling with today’s increasingly complex and miniaturized products.
With human inspectors potentially missing up to 40% of flaws and traditional AOI systems generating high rates of false positives, manufacturers need solutions that match modern production demands.
AI-powered inspection bridges this gap, offering advanced defect detection that maintains accuracy even as products and processes grow more intricate.
The results speak for themselves – with proven accuracy rates exceeding 99%.
We’ll reveal how AI is not just the future of optical inspection but a necessary evolution to meet today’s manufacturing demands.
Key Notes
- Machine learning and neural networks achieve 99% defect detection rates through adaptive pattern recognition.
- Real-time data processing enables immediate defect alerts and proactive maintenance scheduling.
- Volkswagen’s implementation shows significant reductions in downtime and improved production efficiency.
- Initial investment and skilled personnel requirements pose key challenges for smaller manufacturers.
The Current Landscape of Automated Optical Inspection
In manufacturing, precision is a critical goal. Automated Optical Inspection (AOI) plays a crucial role by using advanced optics and image processing to scrutinize products for defects.
Think of AOI as a vigilant overseer. It captures images of products, compares them against predefined standards, and identifies any deviations for further review.
But let’s break it down:
- Image Acquisition: High-resolution cameras paired with optimal lighting conditions capture detailed images from multiple angles. This method ensures that even the smallest defects are visible.
- Image Processing: The system analyzes these images against a set of standards, utilizing powerful algorithms to detect discrepancies that may indicate potential quality issues.
- Defect Classification: After defect detection, the system categorizes these defects by type and severity, providing actionable insights that allow for immediate corrective measures.
Traditional vs. Modern Inspection Techniques in Manufacturing
The shift from manual to automated inspections has brought about considerable advancements in quality control.
Traditional methods relied on skilled inspectors, who, despite their expertise, were limited by human variability and fatigue.
Research has indicated that human inspectors might miss up to 40% of flaws due to these constraints.
In contrast, modern AOI systems:
- Ensure Consistency and Speed: Automated systems eliminate human error, providing lightning-fast inspections that don’t vary with shifts or fatigue.
- 2D vs. 3D Imaging: While initial AOI systems focused on 2D imaging for surface inspections, advances have introduced 3D imaging. This provides depth perception, useful for detecting issues like improper solder joints or component deformation.
- AI Integration: AI enhances defect detection rates and efficiency in AOI systems. Unlike traditional systems with fixed rules, AI-driven solutions learn and adapt in real-time, ensuring accuracy in dynamic production environments.
The Role of AI in Enhancing AOI Systems
How AI Improves Accuracy and Efficiency
AOI has always been pivotal in maintaining high-quality standards in manufacturing.
But the integration of AI takes this to another level. We see AI not just as an improvement but a game-changer in how AOI systems operate.
Enhanced Defect Detection
AI-driven AOI systems apply complex algorithms to analyze image data with unparalleled precision.
These systems handle intricate patterns and anomalies that were once too subtle or complex to detect manually. By learning from diverse datasets, AI systems reduce false positives and negatives, achieving defect detection rates often exceeding 99%.
Adaptive Learning
AI-powered systems continuously learn and adapt. Unlike traditional systems that require manual updates for every new product version, AI systems adjust on the fly.
This flexibility means they can handle varied product lines without significant downtime, making them invaluable in dynamic production environments.
Real-Time Feedback
Speed matters and AI provides it.
With edge computing capabilities, AI models process data instantaneously, allowing for real-time defect identification and immediate corrective actions.
This rapid response reduces the risk of defective products progressing through production, thus saving time and resources.
Key AI Technologies Used in AOI
Three main AI technologies underpin the success of modern AOI systems:
1. Machine Learning
Machine learning uses large datasets to train models, enabling them to identify defects with increasing accuracy.
These models evolve by learning from previous inspections, improving their performance over time.
2. Neural Networks
Specifically, Convolutional Neural Networks (CNNs) are crucial for processing and analyzing image data.
CNNs excel in extracting features from images, which is essential for detecting complex defects in detailed assemblies like printed circuit boards (PCBs). They operate by recognizing hierarchical patterns which traditional methods might miss.
3. Computer Vision
Computer vision algorithms help machines interpret visual data.
By refining image quality through techniques like noise reduction and contrast enhancement, these algorithms improve the visibility of potential defects.
Computer vision enhances the capability of AOI systems to identify issues quickly and accurately.
Key Advantages of AI-Powered AOI
Improved Defect Detection Rates
We know that catching defects before products leave the production line is critical. AI-powered AOI systems excel in spotting these issues early.
Also, by leveraging deep learning algorithms, these systems identify even the most subtle defects, such as micro-cracks or component misalignments, which traditional methods might miss.
Here’s how they achieve it:
- Complex Pattern Recognition: Unlike conventional methods, AI systems aren’t easily fooled by complex surfaces or intricate designs. They recognize patterns and deviations with high precision, ensuring products meet quality standards.
- Consistent Performance: With AI, there’s no worry about fatigue or oversight. Inspection systems maintain high performance, ensuring that no defect goes unnoticed, regardless of production speed.
Reduced Human Error and Labor Costs
Besides accuracy, AI introduces consistency that manual inspection often lacks. Human inspectors, while skilled, can have off days or get tired, which can lead to errors.
- Elimination of Subjectivity: By removing the human element from the equation, AI ensures a standardized inspection process. It’s all about consistent criteria and objective results, which significantly reduces the error rate.
- Cost Efficiency: With automation taking the helm, manufacturers can redirect human resources to more strategic tasks. AI systems lower labor costs as they reduce the need for large inspection teams, cutting down on training expenses and associated human resource burdens.
Real-Time Data Processing and Analysis
Speed is of the essence. AI-powered AOI systems offer not just faster inspections but smarter ones.
They provide insights on the fly, which is invaluable in a high-paced production environment.
- Instantaneous Reporting: When a defect is detected, the system flags it immediately. This means quicker responses and less downtime, as manufacturers can address issues without delay.
- Data-Driven Decision Making: The real-time data these systems generate is a goldmine for process improvement. Manufacturers can analyze inspection results to identify recurring issues, tweak production processes, and ultimately enhance product quality.
Use Case: Volkswagen’s AI AOI in Smart Manufacturing
In the highly competitive automotive industry, Volkswagen is taking significant strides to enhance manufacturing efficiency and product quality through AI-powered AOI.
By shifting from traditional methods to advanced, data-driven systems, Volkswagen is addressing common manufacturing challenges such as downtime, bottlenecks, and quality control issues.
Key Strategies in AI-Powered AOI Implementation:
1. Predictive Maintenance:
Volkswagen employs AI algorithms that analyze historical data from production equipment. This enables the identification of potential failures before they occur.
By monitoring indicators like vibrations and temperature anomalies, the company can schedule proactive maintenance, reducing unexpected downtime and ensuring an uninterrupted production flow.
2. Automated Quality Control:
Utilizing computer vision systems with AI, Volkswagen automates the inspection of automotive parts throughout the assembly line.
High-resolution cameras capture images of components, which AI models then analyze in real-time.
This process allows for the detection of even minute defects that might go unnoticed by human inspectors, ensuring that each product consistently meets stringent quality standards.
3. Workflow Optimization:
AI also plays a pivotal role in refining production processes. By simulating various scenarios, AI identifies the most effective workflows, thereby minimizing waste and maximizing efficiency.
Real-time data analytics adjust operations dynamically, allowing Volkswagen to respond quickly to changes in demand or production conditions.
Quantifiable Benefits of AI-Powered AOI:
- Reduced Downtime and Costs: Proactive measures in predictive maintenance drastically cut the chances of costly interruptions.
- Enhanced Product Quality: AI systems not only catch defects early but also maintain high standards throughout the manufacturing process.
- Increased Production Efficiency: The automation of quality checks boosts output without compromising quality, contributing to greater overall productivity.
By integrating AI technologies into its manufacturing practices, Volkswagen demonstrates how AI-powered AOI systems can revolutionize quality control.
This strategic approach not only improves product reliability but also enhances operational efficiency—demonstrating Volkswagen’s commitment to leading the automotive industry through innovation.
Challenges and Considerations in AI AOI
While AI-powered AOI systems offer remarkable benefits in enhancing quality control and operational efficiency, there are also significant challenges and considerations that manufacturers must address when implementing these technologies.
Limitations of Current AI Technologies in AOI
Data Dependency
AI systems, particularly those leveraging machine learning, rely heavily on quality data for training.
If the datasets used for training are insufficient or biased, the accuracy of defect detection can be compromised.
This makes a commitment to data quality and comprehensive labeling essential for effective implementation.
Complexity of Algorithms
The AI algorithms that power AOI systems can become complex and difficult to interpret.
This lack of transparency can lead to challenges in troubleshooting and refining the systems, particularly if users do not have a deep technical background in AI.
Adaptability to Variations
While AI systems are designed to learn and adapt, substantial changes in production processes or product designs can necessitate further training.
This requirement for ongoing adjustment can be time-consuming and resource-intensive, especially in fast-paced environments where designs frequently evolve.
Implementation Barriers and Cost Considerations
High Initial Investment
Implementing AI-powered AOI systems often requires a significant upfront investment in hardware, software, and training.
Companies must weigh these costs against the potential long-term savings and efficiencies to ensure a sound financial strategy.
Need for Skilled Personnel
Successfully integrating AI technologies into manufacturing operations typically necessitates skilled personnel who understand both the technology and the manufacturing processes.
This demand for expertise can strain resources, particularly for smaller manufacturers who may not have access to such talent.
Integration with Existing Systems
Merging AI-powered AOI with current manufacturing systems can be a complex task.
Companies often face compatibility issues that require additional investments or adjustments, leading to potential disruptions in normal operations during the transition phase.
Frequently Asked Questions
What industries can benefit from AI AOI systems?
AI AOI systems are versatile and can benefit a range of industries, including electronics, automotive, pharmaceuticals, and aerospace.
These systems enhance quality control by detecting defects in various components and assemblies, leading to improved product reliability.
How does AI contribute to reducing operational costs in manufacturing?
By implementing AI-powered AOI systems, manufacturers can automate inspection processes, which reduces the need for extensive manual labor. Additionally, these systems minimize waste through early defect detection, lowering costs associated with rework and material loss.
What role does data play in the effectiveness of AI-powered AOI?
Data is critical in training AI algorithms to recognize defects accurately. High-quality, diverse datasets enable the systems to learn effectively, improving their ability to identify anomalies in real-time and adapting to new production environments seamlessly.
How can manufacturers prepare their workforce for AI integration in AOI?
Manufacturers can prepare their workforce by investing in training programs focused on AI technologies and data analytics. By developing employees’ skills in managing and operating AI systems, companies can ensure a smoother transition and better adoption of these advanced technologies in their processes.
Conclusion
As manufacturing complexities continue to rise, traditional AOI systems face challenges that hinder operational efficiency.
However, the integration of AI into the AOI framework is transforming the future of optical inspection.
Companies like Volkswagen exemplify this shift by employing AI-driven systems that enhance defect detection and streamline manufacturing processes.
AI’s capacity for real-time data analysis and adaptive learning not only improves accuracy but also enables faster, more efficient quality control.
To stay competitive, manufacturers must embrace these advancements. Adopting modern technology not only enhances inspection standards but also paves the way for greater productivity and reduced costs.
Now is the time to harness the power of AI in optical inspection and elevate your manufacturing capabilities.